9.1.- Aplicación de la Tecnología
9.1.1.-
Polaridad
9.1.2.-
Niveles de intensidad y tiempo de impulso
9.1.3.-
Elección del tipo de limpieza
9.1.4.- Recopilación
de datos
9.1.5.- Diseño
de los electrodos
9.1.6.-
Dimensionamiento de los electrodos
9.1.7.-
Cálculo del tiempo de erosión
9.1.-
Aplicación de la Tecnología
Todo proceso de mecanizado
por Electroerosión se debe planificar en arreglo a los siguientes puntos:
-
Problema a resolver.-
En primer lugar se debe saber perfectamente cuál es el problema a
resolver, fijando las condiciones siguientes:
- La rugosidad media o máxima con que debe quedar terminada la pieza.
- El material de la pieza y su tratamiento.
- El número de piezas a realizar.
- La conicidad final con que se debe terminar el proceso.
- La preparación de la pieza tanto antes de realizar los tratamientos
térmicos como antes de realizar el proceso.
Con todo ello se debe realizar un plano de la pieza acabada, perfectamente
acotado, con las tolerancias y la rugosidad exigidas.
-
Regímenes de trabajo.-
En segundo lugar se deben de determinar el número de regímenes de
trabajo, que en general y dada la potencia de la máquina ONA - A 118
(que tomamos de ejemplo), deberán de ser como máximo dos: régimen
de desbaste y régimen de acabado. Puede haber casos en los que sea
suficiente un sólo régimen de mecanizado. Cuando son dos, las medidas
de los electrodos para cada uno de dichos regímenes varían ligeramente
en función de los datos de las tablas de Tecnología.
Se debe de preveer que entre ambos regímenes no
exista una excesiva diferencia de rugosidad. Se recomienda en principio
que dicha diferencia expresada en números de rugosidad VDI no sea
mayor de 8 a 12 Nr. Realmente se debería de hacer un estudio que comparase
el coste del segundo electrodo con el coste total de la operación,
de tal manera que se obtuviera un resultado acerca de saber si es
más conveniente dos regímenes de trabajo (desbaste y acabado) o uno
sólo, habiendo preparado previamente la pieza por medios mecánicos.
Las curvas y tablas de Tecnología muestran la rugosidad
de cada proceso, expresada como número de rugosidad según la norma
VDI 3400, o la rugosidad total expresada en micras, y relacionada
con la velocidad de mecanizado que se desea obtener.
-
Material del electrodo.-
En tercer lugar se debe elegir el material de los electrodos. Como
en general el material de la pieza de los ejercicios que se realizan
a continuación es acero templado para matrices, el material de los
electrodos se deberá elegir entre el cobre electrolítico (E-Cu) y
grafito (C). Además para la mecanización del acero se puede utilizar
el Cuprotugsteno, el Cuprografito, el acero y otros materiales según
se ha visto en el capítulo 7.
Normalmente se deberá de elegir de entre los dos
primeros (Cu y Grafito), en función del precio, del rendimiento, del
peso del electrodo y de la facilidad de mecanizado. Se debe de tener
muy en cuenta el tipo de trabajo a realizar, pues es diferente la
mecanización de un agujero pasante, en cuyo caso no es importante
el desgaste y sí el arranque de material o la mecanización de un agujero
ciego en el que se debe de reproducir perfectamente la forma del electrodo,
en cuyo caso será importante obtener el mínimo desgaste posible, a
expensas de un menor arranque.
En general se deberá de elegir el material del
electrodo comparando las curvas de tecnología, y viendo los arranques,
los desgastes y la rugosidad de acabado.
-
Reglaje del generador.-
En cuarto lugar se deben de determinar las variables de reglaje del
generador por el orden siguiente:
9.1.1.-
Polaridad
Teniendo en cuenta el material
de la pieza a erosionar y el material del electrodo, se elegirá la polaridad
según la Tabla 9.1 adjunta.
Tabla
9.1
POLARIDAD DEL ELECTRODO Y PIEZA A EROSIONAR |
Pieza a erosionar |
Electrodo |
Polaridad del
electrodo |
Observaciones |
Acero |
Cobre |
+ |
|
Acero |
Grafito |
+ / - |
|
Hierro fundido |
Cobre |
+ |
|
Cobre |
Grafito |
- |
|
Metal duro |
Cobre |
- / + |
Según composición del
metal duro |
Acero |
Acero |
- / + |
Cambiando periódicamente |
Aluminio
Zamak
Latón |
Cobre |
+ |
|
Acero |
Wolframio |
+ |
|
Acero |
Sparkal |
+ |
|
Metal duro |
Cobre |
- |
|
Cobre |
Cobre |
+ |
|
Se ha de tener en
cuenta que en el mecanizado de acero con acero se debe ir cambiando periódicamente
la polaridad con el fin de obtener el menor desgaste posible en el electrodo.
También se debe de
contar con que en la combinación acero para la pieza y grafito para el
electrodo la tabla adjunta marca como polaridad la positiva. No obstante
comparando las tablas B (Electrodo C + , pieza Acero -), con las tablas
C (Electrodo C - , pieza Acero +), se pueden obtener las conclusiones
siguientes:
-
En el caso de grafito (+) los desgastes
son en general muy pequeños, mientras que los arranques son algo mayores
que en el caso de electrodo de cobre positivo.
-
En el caso de electrodo de grafito
(-) los arranques son mucho mayores que en el caso de grafito (+),
pero los desgastes oscilan entre el 17 y 60 por 100. Así mismo las
rugosidades son mayores en este segundo caso. Por ello este segundo
régimen (grafito negativo) se utilizará solamente en el caso de que
el desgaste no tenga la más mínima importancia, como puede ser el
caso de un agujero pasante, dándole al electrodo mayor longitud que
en otros casos. Sin embargo en el caso de querer obtener una buena
reproducción de formas se debe de recurrir a la polaridad positiva.
9.1.2.-
Niveles de intensidad y tiempo de impulso
El nivel de intensidad
y de excitación se debe de escoger teniendo en cuenta la superficie mínima
marcada en las tablas de Tecnología para cada régimen. En los procesos
de desbaste éste debe ser el único criterio a seguir. Por ello se debe
de calcular en todos los casos la superficie frontal de erosión antes
de elegir el régimen de intensidad y de excitación.
En régimen de acabado se elegirá aquel reglaje que
permita obtener la rugosidad deseada, marcada en el enunciado del problema,
combinándolo con la superficie mínima exigida por las tablas.
En cuanto al tiempo de impulso (ti) se debe de elegir
al mismo tiempo que las variables anteriores, en función del rendimiento
(arranque y desgaste) y de la rugosidad final requerida.
9.1.3.-
Elección del tipo de limpieza
Como hemos visto en el
Capítulo 4, la limpieza se puede realizar de diferentes maneras. Las dos
principales son las de presión o aspiración, y ambas formas se pueden
realizar a través de la pieza o de la herramienta o electrodo. Además
la máquina ONA - A 118 que vamos a usar en los ejercicios, dispone de
un temporizador tal y como ya se ha descrito.
Según sea la forma del electrodo y pieza, y según sea
el tipo de trabajo a realizar (agujeros pasantes o ciegos), se elegirá
uno de los cuatro tipos descritos, teniendo en cuenta además la conicidad
que se desee obtener. No obstante es la experiencia en un tipo determinado
de trabajo, la que suele aconsejar el tipo de limpieza. Se ha de tener
en cuenta que la forma elegida influye en la preparación de la pieza y/o
del electrodo.
En cuanto a la presión del fluido dieléctrico se debe
de regular de forma que la máquina funcione de forma estable, y es un
parámetro que debe irse regulando según lo aconseje la máquina. No obstante
las tablas de Tecnología dan valores indicativos sobre dicha presión.
9.1.4.-
Recopilación de datos
Una vez enunciado el trabajo
a realizar, con la superficie a obtener, fijados los regímenes de mecanizado,
materiales del electrodo, reglaje del generador y tipo de limpieza, se
debe rellenar la ficha de mecanizado que a continuación se presenta, u
otra que el operario idee para ello.
Dicha ficha se debe rellenar completa extrayendo los
datos necesarios de las Tablas de Tecnología. De esta manera se pueden
tener recopilados dichos datos, lo que facilita los cálculos del dimensionamiento
de electrodos y del tiempo que se va a emplear en la operación tanto en
desbaste como en acabado. Además y si el espacio lo permite se puede realizar
un plano de la pieza a mecanizar y otro del electrodo, con lo cual se
tendrán en una sola hoja todos los datos manejados en un proceso determinado.
ELECTROEROSION
FICHA DE TRABAJO
EJERCICIO NUMERO
|
Datos
del problema |
Electrodo núm. |
. |
. |
. |
. |
Operación (Desbaste: D, Acabado: A) |
. |
. |
. |
. |
Material electrodo |
. |
. |
. |
. |
Material pieza |
. |
. |
. |
. |
Número de piezas a realizar |
. |
. |
. |
. |
Estado superficial deseado (Nr) |
. |
. |
. |
. |
Rugosidad total (µm) |
. |
. |
. |
. |
Reglaje
Generador |
Polaridad electrodo |
. |
. |
. |
. |
Nivel intensidad Excitación |
. |
. |
. |
. |
Tiempo impulso Puntos (ti) |
. |
. |
. |
. |
Tiempo pausa Puntos (to) |
. |
. |
. |
. |
K.C. Puntos |
. |
. |
. |
. |
Limpieza |
Forma |
. |
. |
. |
. |
Presión (bar) |
. |
. |
. |
. |
Datos
para cálculos |
Menor medida por lado (mm) |
. |
. |
. |
. |
Espacio entre electrodo y pieza (mm) |
. |
. |
. |
. |
Desgaste volumétrico relativo sV
(o/o) |
. |
. |
. |
. |
Arranque Vw (mm3/min) |
. |
. |
. |
. |
Superficie mínima (mm2) |
. |
. |
. |
. |
Superficie a trabajar (mm2) |
. |
. |
. |
. |
Volumen a arrancar (mm3) |
. |
. |
. |
. |
Estimación tiempo mecanizado (min) |
. |
. |
. |
. |
Resultados
finales |
Tiempo real de mecanizado (min) |
. |
. |
. |
. |
Superficie obtenida (Nr) |
. |
. |
. |
. |
Observaciones |
. |
. |
9.1.5.-
Diseño de los electrodos
Cuando los agujeros son
pasantes y cilíndricos, los electrodos de desbaste y acabado pueden fabricarse
o bien escalonados o bien independientes entre sí (Fig. 9.1
y Fig. 9.2).
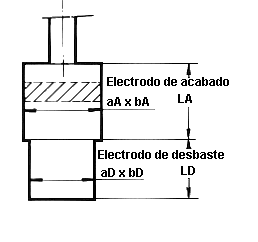 |
|
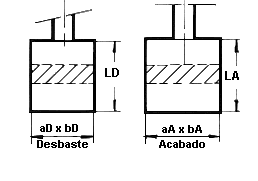 |
Fig. 9.1
Electrodos de desbaste y acabado escalonado |
|
Fig. 9.2
Electrodos de desbaste y acabado independientes entre si |
El caso de electrodos
escalonados tiene las ventajas siguientes:
-
El centrado de ambos electrodos
se realiza en una sola operación para ambos.
-
En caso de ser de cobre, se puede
obtener por mecanizado convencional un electrodo de longitud LD
+ LA, y con las medidas del electrodo de acabado (aA
x bA), y después reducir la medida de la parte de desbaste
con ácido nítrico.
Sin embargo, en caso de que ambos electrodos sean
de grafito, dichas medidas se deberán obtener por mecanizado.
Los posibles inconvenientes
de los electrodos escalonados son:
-
No se pueden elegir dos materiales
diferentes para las operaciones de desbaste y acabado.
-
La longitud del electrodo de desbaste
ha de ser superior a la altura a mecanizar, lo que hace imposible
el empleo de este tipo de electrodos en agujeros de mucha longitud.
9.1.6.-
Dimensionamiento de los electrodos
El dimensionamiento de
los electrodos se hace de diferente manera si se trata del electrodo de
desbaste o del de acabado.
En caso de desbaste se utilizará el valor dado en la
tabla como "MEDIDA MENOR POR LADO" (M.m.l.). Esta medida no
tiene que ver con la suma Gap más Rugosidad total (g + Rt). La Medida
Menor por Lado es un margen de seguridad para trabajos en malas condiciones
de limpieza, desconocimiento de materiales, distinto voltaje en la red
y fijaciones no muy precisas de los electrodos.
La Fig. 9.3 da una idea muy precisa
de lo que ocurre en un proceso de desbaste. De ella se deduce cómo se
puede calcular la Medida del Electrodo de Desbaste (M.ED).
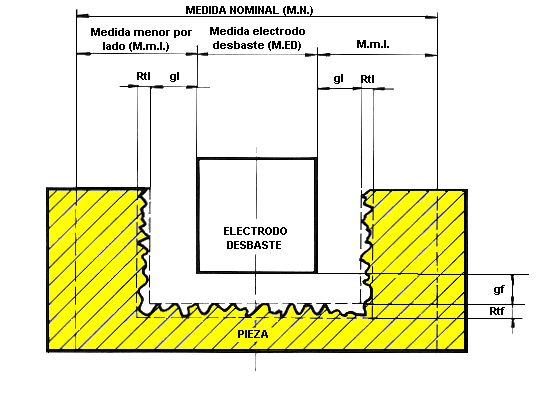 |
Fig. 9.3 Proceso
de desbaste |
Medida electrodo desbaste: Medida
nominal - 2 x Medida menor por lado en desbaste
M.ED = M.N - 2
x M.m.lD
Se ha de tener en
cuenta que tanto la medida menor por lado como el gap contornean totalmente
la pieza tal y como aparece en la Fig. 9.4, que representa
a un electrodo penetrando en una pieza, visto desde arriba.
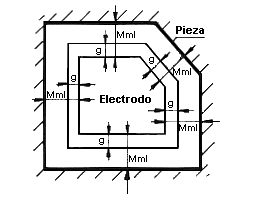 |
Fig. 9.4 |
En cuanto al cálculo
de las medidas del electrodo de acabado pueden ocurrir dos casos:
-
Que se vaya a realizar una operación
de pulido después del proceso de acabado, como puede ocurrir en el
caso de algunos moldes.
-
Que la pieza se vaya a dejar acabada
tal y como salga del proceso de erosión, como es el caso de las matrices
de corte.
El primero de los
casos se halla representado en la Fig. 9.5.
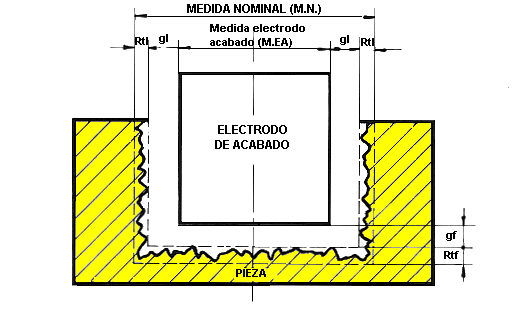 |
Fig. 9.5 Proceso
de acabado, con pulido posterior |
De ella se desprende:
Medida nominal: 2 Rtl + 2 gl + Medida
electrodo de acabado (MEA)
M.N = 2Rtl + 2gl + MEA
Y por tanto la medida del electrodo
será:
MEA = M.N - 2 (Rtl
+ gl)
Dado que en los gráficos
y tablas de Tecnología aparecen la Rugosidad total lateral (Rtl) y el
gap lateral (gl) o bien la suma de ambos, se tienen datos suficientes
para el cálculo del electrodo.
En el caso de que no haya pulido posterior la medida
del electrodo de acabado se calculará:
MEA = M.N - 2 Gap
Se deduce que el
electrodo de desbaste es menor que el de acabado.
9.1.7.-
Cálculo del tiempo de erosión
1. Terminología a utilizar.
Para el cálculo de
los tiempos de erosión se empleará la siguiente terminología:
h.-
Altura a mecanizar en orificios (mm).
p.-
Perímetro mecanizado (mm).
Vw.-
Arranque específico de material (mm3/min).
Sd.-
Desarrollo de las superficies en cavidades tridimensionales o no.
sV.-
Desgaste volumétrico relativo (tantos por 100).
sV = (Volumen arrancado del electrodo / Volumen arrancado
de la pieza) x 100
M.N.- Medida nominal.
b.-
Anchura de banda o corona en el proceso de acabado.
tM.-
Tiempo total de mecanizado. Suma de los tiempos de desbaste y acabado
si hay dos electrodos.
|
Desbaste |
Acabado |
Medida menor por lado |
MmlD |
MmlA |
Gap lateral |
gD |
gA |
Rugosidad total lateral |
RtD |
RtA |
Medida del electrodo |
M.ED |
M.EA |
Longitud del electrodo |
LD |
LA |
Tiempo de mecanizado |
tD |
tA |
Superficie frontal de erosión |
SD |
SA |
Volumen a arrancar |
VD |
VA |
Siempre que aparece
el subíndice D se refiere a la operación de desbaste, y siempre que aparece
el símbolo A se refiere a la operación de acabado.
2. Tipos de operaciones a realizar.
Los tipos de orificios
que se pueden realizar principalmente por el proceso de Electroerosión
son cuatro:
-
Orificios cilíndricos pasantes.-
Son aquellos en los que, además de pasar el electrodo de lado a lado
de la pieza, el electrodo tiene la misma sección transversal a lo
largo de toda su longitud (Fig. 9.6). En ellos la
limpieza se realiza normalmente por presión o aspiración a través
de la pieza por medio de un taladro previo a la erosión.
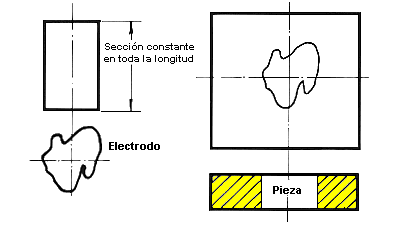 |
Fig. 9.6 Orificios
pasantes cilíndricos |
-
Orificios pasantes tridimensionales.-
Son aquellos en los que la sección del electrodo no permanece constante
(Fig. 9.7). En este caso la limpieza se realiza también
normalmente a través de la pieza, bien por presión o por aspiración.
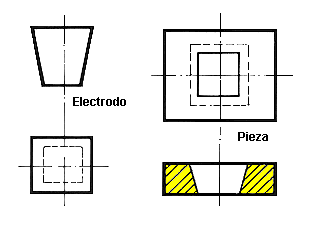 |
Fig. 9.7 Orificio
pasante tridimensional |
-
Cavidades cilíndricas ciegas.- Corresponden
al caso a) pero sin que el agujero sea pasante. La limpieza se suele
realizar por presión o aspiración a través del electrodo.
-
Cavidades ciegas tridimensionales.-
Son aquellas del caso b) pero en las que un agujero no llega a ser
pasante. La limpieza en este caso también se suele realizar a través
del electrodo.
En todos los casos,
para el cálculo de tiempo de erosión tanto en desbaste como en acabado,
es importante saber, tanto el volumen de la cavidad a realizar, como el
desarrollo de la superficie lateral. Los cálculos son muy parecidos en
todos ellos aunque existen ligeras diferencias que se observarán en los
ejemplos.
3. Cálculo del tiempo de la
operación de desbaste.
Todo cálculo de tiempo
de mecanizado en el proceso de Electroerosión es difícil de determinar,
ya que los datos sobre arranque de material que dan las tablas de Tecnología
no son totalmente exactos. Cada proceso de Electroerosión se da en condiciones
distintas a otro y por ello los tiempos de dos operaciones idénticas no
coinciden. Los datos de las tablas son medias de diversos casos realizados
en laboratorio. No obstante la aproximación en la mayoría de los casos
suele ser muy buena. Lo mismo ocurre con el desgaste y la rugosidad.
El tiempo de mecanizado en desbaste se calcula mediante
la fórmula:
tD
(min) = VD (mm3) / VW (mm3/min)
A su vez el volumen a arrancar en el caso de desbaste
de agujero cilíndrico pasante o no, es:
VD
(mm3) = SD (mm2) x h (mm)
Si la cavidad es tridimensional (pasante o no pasante)
se debe de recurrir a fórmulas geométricas apropiadas.
4. Cálculo
del tiempo de la operación de acabado.
-
Caso de orificios
cilíndricos pasantes.
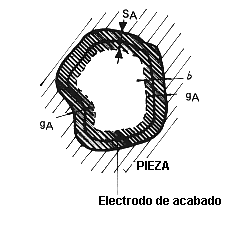 |
Fig. 9.8 |
Suponiendo una
forma cualquiera (Fig. 9.8), la línea punteada corresponde
a la que ha quedado en la pieza tras la operación de desbaste. La
parte sombreada corresponde a la superficie frontal de erosión en
acabado (SA). En la Fig. 9.9 se ve ampliada
y la forma de calcular la anchura (b) de la parte sombreada. Dicha
anchura multiplicada por el perímetro de la pieza dará como resultado
SD.
Se cumple
MmlD
+ (RtA/2) = gD + (RtD/2) + b
b = MmlD - gD
- (RtD - RtA) / 2
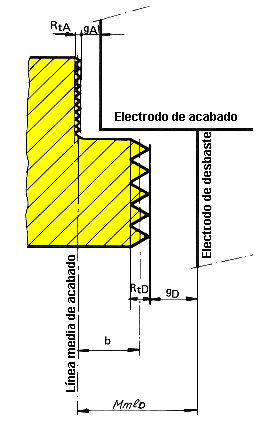 |
Fig. 9.9 Cálculo
del proceso de acabado
|
Se han considerado
las líneas medias de acabado y desbaste. La parte entre ambas corresponde
al material que se debe arrancar. Se ha de tener precaución y poner
todos los números en mm.
Superficie frontal
SA (mm2)
= b (mm) x p (mm)
Volumen a arrancar
VA (mm3)
= SA (mm2) x h (mm)
Una vez calculado el volumen se procede como en
la operación de desbaste.
Tiempo de acabado
tA (min)
= VA (mm3) / VW
-
Caso de cavidades cilíndricas no
pasantes.
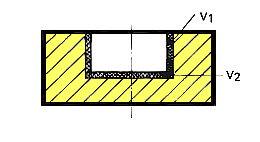 |
Fig. 9.10
Cavidad cilíndrica no pasante |
El procedimiento
es muy parecido al anterior. En la Fig. 9.10, el
volumen a arrancar se halla rayado en cruz. El vacío que aparece es
el que ha quedado en la operación de desbaste. V1 representa
el volumen a arrancar que se puede calcular de la misma forma que
en el caso anterior. V2 representa el volumen del fondo
de la cavidad, que se debe de procurar que sea el mínimo posible.
No obstante se ha de profundizar lo suficiente como para pulir la
cavidad, o sea una cantidad mayor que la suma del gap y la rugosidad
total del proceso de desbaste. Realizado el cálculo del volumen total
se procede como en el caso a).
-
Caso de agujeros pasantes no cilíndricos.
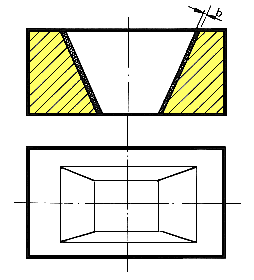 |
Fig. 9.11
|
En este caso
es importante conocer la superficie lateral del orificio o superficie
desarrollada (Sd), que multiplicacada por la anchura (b),
dará como resultado el volumen a mecanizar (Fig. 9.11).
VA (mm3) = Sd (mm2)
x b (mm)
-
Caso de cavidades no cilíndricas.
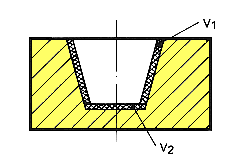 |
Fig. 9.12
|
Para el cálculo
de volumen a arrancar en el proceso de acabado se deben de sumar los
volúmenes V1 (caso c, agujeros pasantes no cilíndricos)
y el volumen V2 (caso b, cavidades cilíndricas no pasantes)
(Fig. 9.12).
5. Consideraciones para el caso
de cavidades y orificios no cilíndricos.
En estos casos, al
ser la sección frontal de erosión variable conforme avanza el proceso
se pueden elegir varias formas de actuación. Se puede elegir uno solo
o dos electrodos.
En caso de elegir dos electrodos (uno para desbaste
y otro para acabado), el régimen de desbaste se realizará cambiando de
régimen, según la superficie de erosión que se vaya presentando en cada
momento, para terminar con el régimen de mayor velocidad de arranque posible.
En el régimen de acabado se elegirá aquel régimen que permita el estado
superficial que se desea. Con el electrodo de desbaste se debe llegar
hasta muy pocas décimas antes de llegar a la profundidad deseada.
A veces se puede realizar el desbaste y el acabado
en el mismo electrodo, dependiendo de la forma que tenga el electrodo.
Para ello se comienza con un régimen determinado, se cambia a regímenes
más fuertes conforme va aumentando la penetración y presentando más superficie
frontal y al final se cambia al régimen de acabado. En este caso el electrodo
se ha de dimensionar con las medidas de acabado.
Otras veces (dependiendo siempre de la forma) se puede
dimensionar el electrodo con las medidas de desbaste, incluyendo la medida
menor por lado, y después realizar el acabado moviendo el carro de la
máquina en ambos sentidos una cantidad que puede ser calculada.
De todas formas en estos casos, de todo tipo de cavidades
y agujeros pasantes no cilíndricos, lo que interesa es la reproducción
más perfecta posible de la forma del electrodo. Por ello siempre se deberá
de elegir regímenes con desgastes relativos mínimos, como pueden ser todos
los marcados en las tablas con sV
< = 0,5 por 100.
Otra nota a tener en cuenta es que en estos casos la
limpieza se ha de hacer normalmente a través del electrodo. Ello da lugar
a que se dificulte algo la operación y se obtenga un rendimiento menor
que el marcado en las tablas.
[ Anterior
| Siguiente | Arriba ]
|